Introduction
Our planet is grappling with immense challenges - from climate change to rising inequality. The large corporates have additional responsibilities of ensuring that the economic endeavours align with societal necessities, owing to the number of lives they touch. Stakeholders, like investors, regulators, customers or employees, expect companies to act as responsible guardians of not just the financial capital, but of natural and social capital as well. A growing number of investors are weaving ESG factors into their investment evaluations, making ESG crucial for attracting capital investments. All these make ESG an essential part of business.
ESG, which stands for Environmental, Social, and Governance, is a framework for evaluating a company's impact on the economy, environment, and people including human rights. It gained prominence in the business world in early 2000s. Leading companies around the world are integrating ESG principles into their core strategies, and PCBL, a global chemical company belonging to RPSG Group, is no exception. ESG is not just a set of guidelines but a commitment to sustainable growth, ensuring that an organisation is environmentally conscious, socially responsible, and governed with integrity.
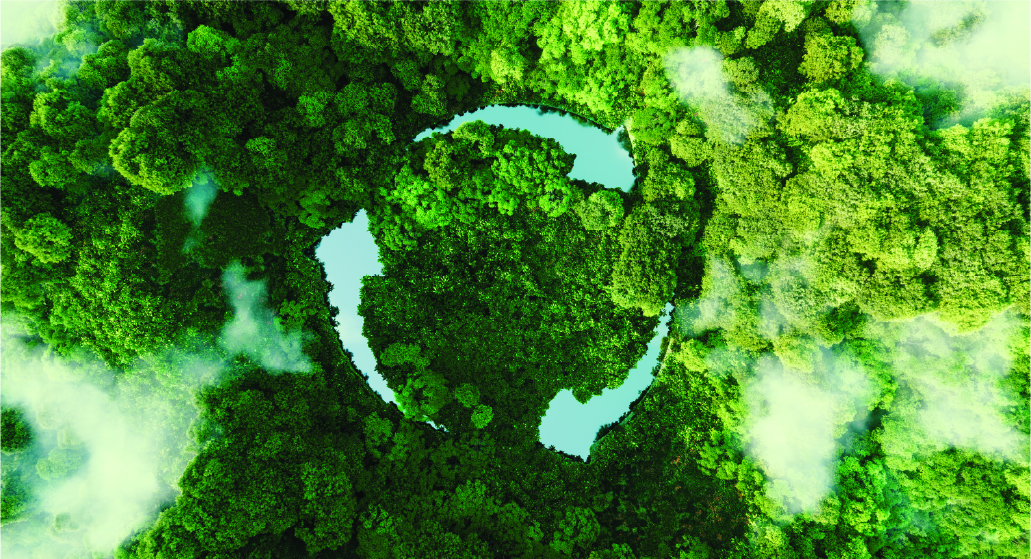
In this Whitepaper, we delve into the ESG practices adopted by PCBL and also explore the universal learnings emanating from these, which can be adopted by other companies. By aligning with ESG standards, PCBL not only showcases its dedication to corporate responsibility but also positions itself as one of the leaders in the chemical industry, ready for the challenges and opportunities of a sustainable future.
Understanding ESG & its Three Pillars
The concept of ESG has been evolving over time, but its formal adoption and integration into investment and corporate practices began in early 2000s. ‘Environment’, ‘Social’, and ‘Governance’, are the three primary 'pillars', that companies had to report under. One significant milestone in the development of ESG reporting was the release of the Global Reporting Initiative (GRI) guidelines in 2000. The guidelines provided a comprehensive framework for companies to report their sustainability and ESG-related information in a structured and standardised way.
1. The Environmental Pillar
This pillar is the most significant from a reporting standpoint. It encompasses prevention of emissions (for example, greenhouse gases, and other emissions like Sulphur oxides, Nitrogen Oxides and particulate matter), optimised resource usage (for example, utilising resources effectively during the production process), and waste management (for example, prevention of landfill accumulation). There’s also an emphasis on water resource conservation and land usage aspects like afforestation and biodiversity.
2. The Social Pillar
Here, companies need to disclose human rights, employee wellbeing and community engagement practices involved in the entire process of producing and delivering the company's products or services. This encompasses all the labour used, from the initial sourcing of raw materials to the final delivery of the product to the consumer.
3. The Governance Pillar
This section focuses on aspects like ethics, shareholders' rights, diversity within boards, executive compensations, and how these compensations align with the company’s sustainability goals. Anti-corruption initiatives are other areas of significance.
4. ESG Timelines in India
In a landmark move in 2020, SEBI mandated 1,000 listed premier entities to incorporate ESG specifics within their annual statements starting from the fiscal year 2021-22. The stipulations encompassed a range of topics, from carbon footprints, waste reduction, energy management and water management to aspects like employee wellbeing, diversity and board structure.
5. ESG Reporting
Over the years, various standards, such as the Global Reporting Initiative (GRI), Sustainability Accounting Standards Board (SASB) and the Task Force on Climate-related Financial Disclosures (TCFD), have played crucial roles in shaping up the ESG reporting and practices. These standards helped to create an improved and structured approach for ESG disclosures, thereby making it more streamlined for the investors to compare the ESG efficiencies of various enterprises.
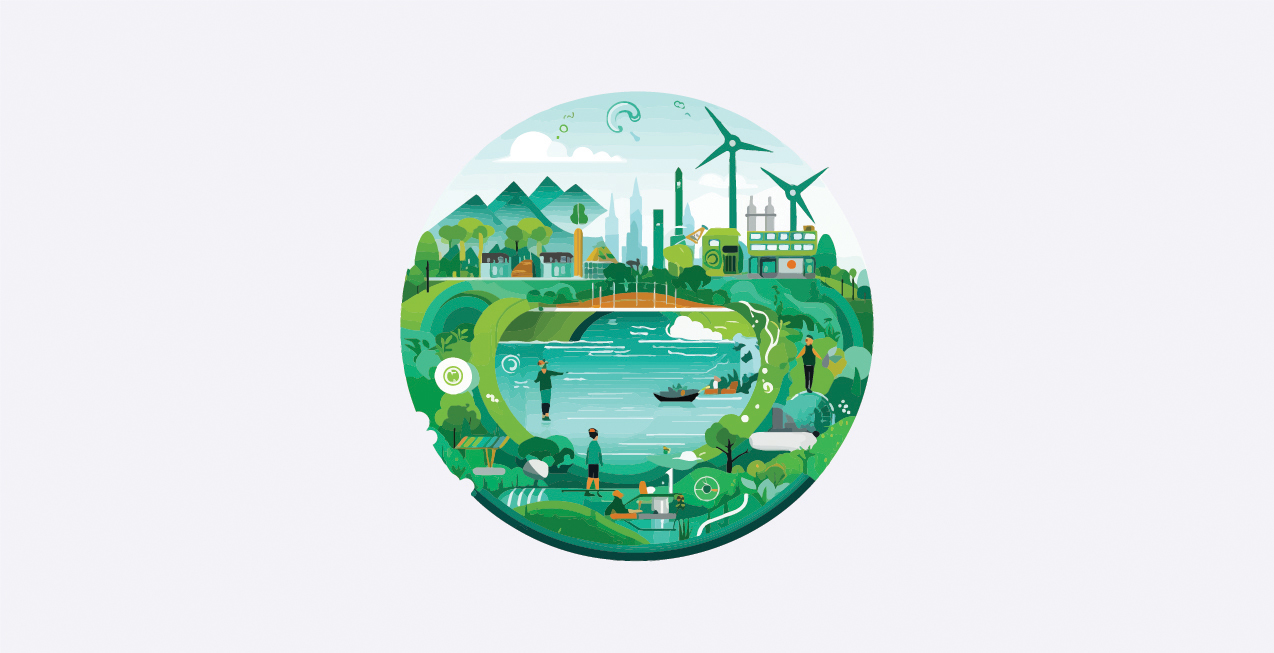
How PCBL Formally Embarked on its ESG Journey
Expert Consultation and Assessment
PCBL (erstwhile Phillips Carbon Black) was the first company in the world to receive carbon credit under Kyoto Protocol of UNFCC in 2004. While PCBL has been an environmentally-conscious company right from its inception, in 2019, an expert external consultant was hired, and a thorough carbon footprint assessment was conducted across PCBL's facilities and offices.
PCBL engaged stakeholders to fine-tune key material topics. Following key areas were identified for putting enhanced focus as part of the company's Environmental, Social, and Governance (ESG) initiatives:
The Environment Pillar
- Greenhouse gas (GHG) emission & energy management
- Solid waste management
- Water management
The Social Pillar
- Health and safety
- Human rights, employee wellbeing & community engagement
The Governance Pillar
- Product stewardship
- Governance & leadership
The Environment Pillar - PCBL’s Initiatives to Protect the Environment
PCBL has taken various initiatives towards protecting the environment by focussing on improving energy efficiency, reducing emissions, conserving water, and managing waste.
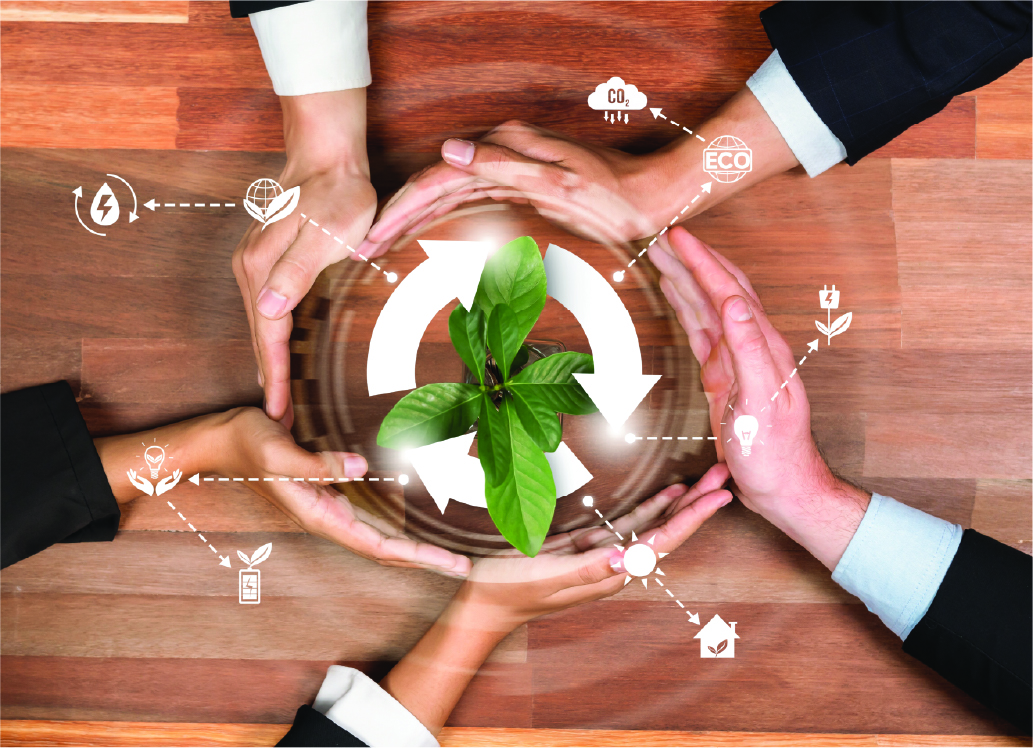
Energy Efficient Manufacturing Process
PCBL has brought energy efficiency throughout its manufacturing process. For example, heat exchangers have been strategically installed at different points in the production chain, specifically at “downstream” stages (later in the process), in order to decrease the need to burn fossil fuels. These heat exchangers help to capture and transfer heat from one part of the process to another, making the overall system energy-efficient and reducing the reliance on fossil fuels.
Investing in Sustainable Technologies to Save Water
The company has implemented rainwater harvesting which resulted in substantial water savings. Rainwater harvesting involves collecting and storing of rainwater in tanks or reservoirs for later use. The collected water is used for horticultural purposes and replenishing groundwater. The company has achieved a significant water saving of 813,000 litres per day. The practice reduces the demand on local freshwater sources, which has a broader positive impact on the community and environment.
PCBL has also made considerable efforts to adopt responsible water management practices. All manufacturing plants are now Zero Liquid Discharge (ZLD) compliant. For example, the waste water produced during manufacturing is treated and recycled into the production process. At the Palej & Mundra facilities, recycled water from the Sewage Treatment Plant is used for horticultural activities, and water from the effluent treatment plant is returned to the Water Treatment Plant for further operational use. The Mundra plant also employs injection-well technology to recharge treated rainwater back into the groundwater system. At the Kochi plant, PCBL has installed a chlorine dioxide (ClO2) generator. Water rejected from the ultra-filtration process is recycled back into the system, achieving a 10% decrease in overall water usage.
Monitoring and tracking of water consumed and saved daily provides PCBL with valuable data which helps the company to identify usage trends, detect anomalies, and benchmark performance against industry standards.
Efficient Waste Management and Utilisation
PCBL maintains a vigilant approach to managing waste by closely monitoring and quantifying the various types of waste generated throughout its operations. For example, a central scrapyard at the Kochi facility helps in the appropriate sorting and disposal of waste materials. Employee trainings are offered across the manufacturing units to raise awareness about waste management. Detailed standard operating procedures (SOPs) for waste management have been created to steer the process. A third-party audit on Zero Waste to Landfill (ZWL) has been conducted at PCBL Durgapur, and other plants will be covered in 2024. This initiative aims to ensure that waste management is carried out robustly and that waste does not end up in landfills.
Rather than treating waste as a mere disposal problem, the company tries to convert waste into resources whenever possible. For example, PCBL has implemented a remarkable initiative that involves generation of electricity from waste gases released during carbon black production. These waste gases are a natural byproduct of the production process and would typically be considered as industrial waste. The heat value of the waste gas, so generated, is utilised to produce electricity.
The electricity thus produced is utilised by the company. Any surplus electricity, which exceeds the company's operational requirements, is fed into the electrical grid, thereby significantly offsetting greenhouse gas emissions. PCBL constantly invests in research and development to find more such innovative ways of converting waste into valuable resources.
Sustainable Transport
PCBL factories are strategically located to meet the demand of the customers. For example, Tamil Nadu, often referred to as the ‘Detroit of India’ because of its thriving automobile industry, has a significant high demand for tyres. Carbon black is a crucial raw material for the tyre manufacturing industry. By setting up a plant in Chennai, PCBL has positioned itself close to its customer base, which reduces the transportation costs and time taken for delivery.
During the transportation of finished goods, PCBL ships materials from the factory closest to the customer. Here too, the company leverages sea routes or segments of sea routes to minimise the distance of shipping its products to customers. All PCBL factories have access to sea ports which help in minimising the environmental impact of longer land-based journeys. Through collaborative approach, PCBL saved 659 tCO2e (tonnes CO2 equivalent) of greenhouse gases in 2023, by shipping with Maersk Eco Delivery.
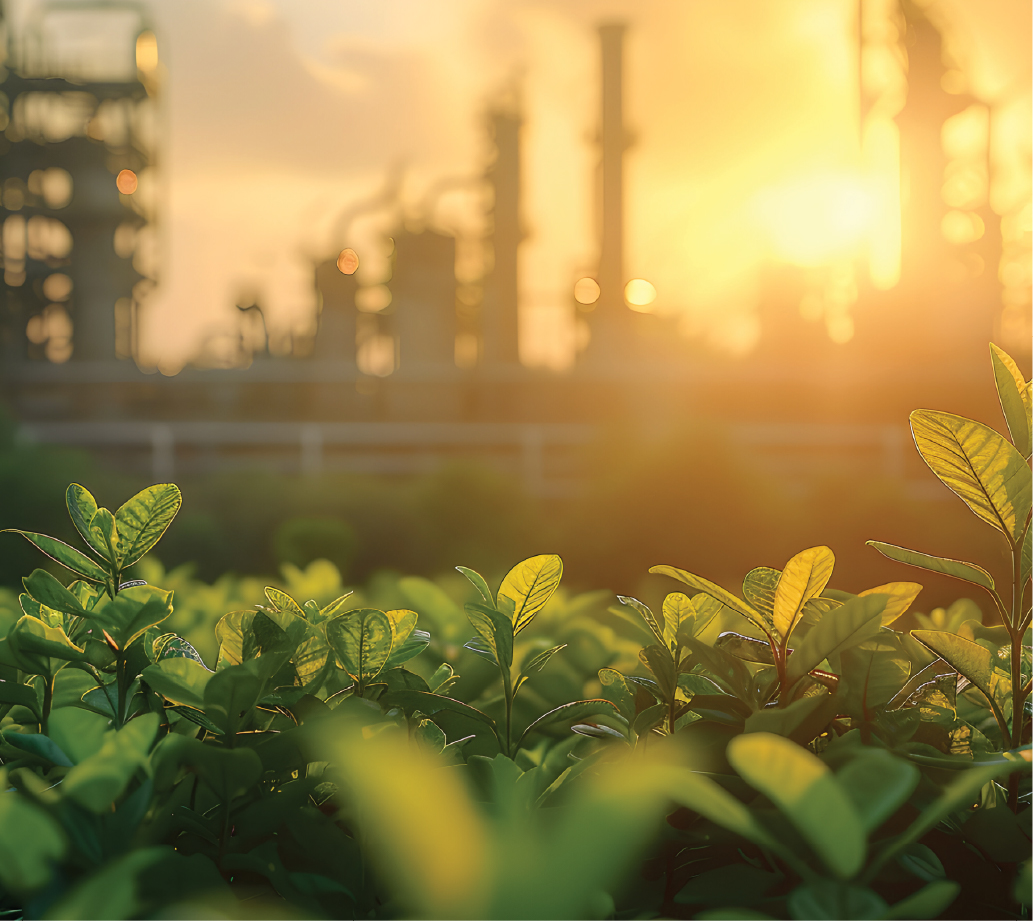
Optimisation of Packing Materials
PCBL has introduced a plastic bag reuse programme which involves the retrieval of used plastic bags from customers for subsequent use in the supply chain. The primary objective is to reduce the environmental impact associated with plastic consumption and disposal.
Another notable initiative is the increase in the "loadability" of plastic packing bags, allowing each bag to carry an additional 5% of the product. This has been achieved through an innovation of increasing the density of the product, thereby accommodating more material in a plastic bag of the same size. Consequently, there was a significant reduction in plastic consumption and an increase in the amount of material transported in a single consignment. Because of this initiative, 7.5 metric tonnes of plastic usage were reduced annually.
Developing Local Suppliers
Sourcing raw materials locally minimises the carbon footprint associated with long-distance transportation. It also creates job opportunities and fosters economic growth in the region, contributing to the community's well-being. PCBL is working on developing local suppliers for sourcing raw materials to create a sustainable and efficient supply chain.
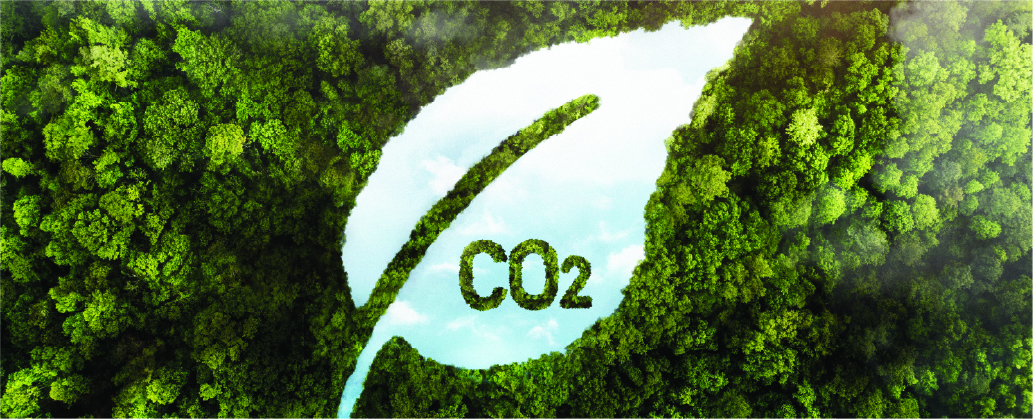
Universal Learnings
- The effectiveness of any sustainable initiative should be measurable. Metrics, like the volume of water saved in the case of rainwater harvesting, provide valuable data that can be used to assess the project's impact and make necessary adjustments.
- Companies that invest in sustainable technologies are often better prepared for future environmental regulations. The effective positioning of technologies especially at bottleneck points can dramatically improve system efficiency. The key is to identify and address them to make the most meaningful impact.
- Instead of viewing waste solely as a problem to be disposed of, it can be seen as a resource waiting to be utilised. Investing in research and development for innovative waste-to-resource strategies can result in groundbreaking methods to convert waste into useful products. Whether it's generating electricity from waste gases or recycling used water, innovation is the cornerstone of turning waste management from a cost centre to a value-creating operation.
- The selection of strategic locations for facilities can significantly impact a company's supply chain. The ultimate goal is to create a supply chain that is not only efficient but also sustainable. The logistics infrastructure plays a vital role in how materials are moved and should be chosen carefully. This not only lowers operational costs but also reduces carbon emissions and the overall environmental impact of the business.
- Having multiple manufacturing or storage locations allows businesses to adopt a multi-point delivery strategy. This means products can be shipped from the facility closest to the customer, reducing the distance they must travel and consequently lowering time taken to deliver, costs and emissions. It also creates jobs and stimulates local economies.
The Social Pillar - PCBL’s Initiatives for People and Communities
The social pillar of ESG represents a critical dimension that evaluates a company's impact on the society and its stakeholders. It encompasses a range of considerations like health and safety of people, diversity and inclusion at workplace, product safety, ethical interactions with customers and suppliers. It reflects a company's commitment to responsible and ethical practices in its interactions with people and communities. PCBL recognises that businesses have a broader societal role beyond profit generation and has taken various initiatives.
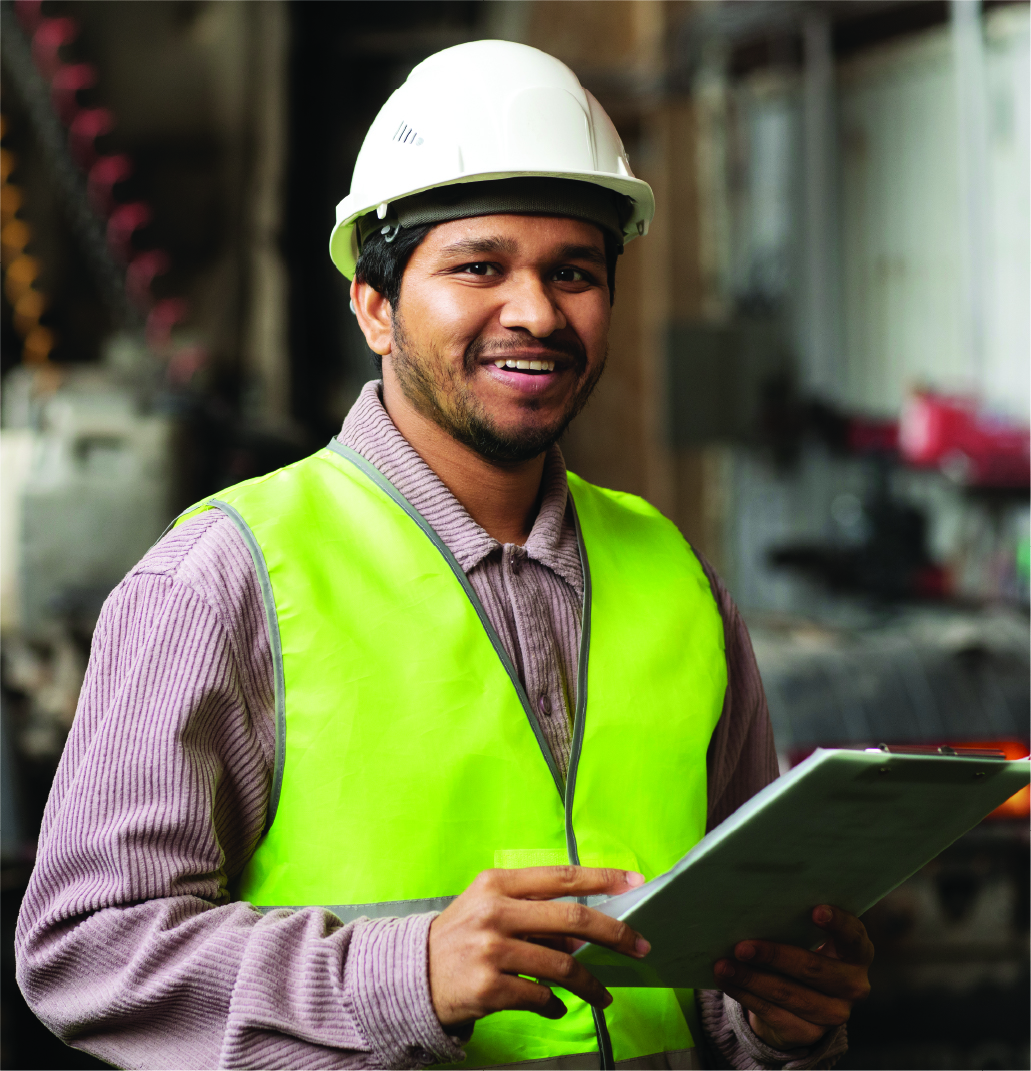
Creating a Healthy and Safe Work Environment
Health and safety are of paramount importance within the operations of PCBL. The company constantly strives to safeguard the well-being of both employees and surrounding communities. PCBL holds ISO 45001:2018 certification and has established occupational health and safety management programme across all its manufacturing facilities. Internal audits by certified auditors help to assess risks and take appropriate actions proactively.
The company has an Environment, Health & Safety (EHS) policy that outlines measures that help to create and maintain safe working environment for everyone - employees, contractors, and vendors, by preventing safety-related incidents and injuries.
PCBL identifies work-related hazards through various techniques such as Hazard Identification and Risk Assessment (HIRA), Hazard and Operability Study (HAZOP), and Job Safety Analysis (JSA). These hazards are reported through the Learning Event (LE) reporting system. The LE system enables the employees to report unsafe conditions, unsafe acts, and near misses. Prior to commencing any job, the workers receive safety briefings. Safety display and caution boards in plant areas are used to educate workers and employees about hazards and safety guidelines. Visitors, customers, and business officials also undergo safety induction before entering plant premises. PCBL has also formed a Safety Committee at all its facilities, headed by the Unit Leader as Chair and the Safety Chief as Secretary, alongside department managers and representatives of contracted workers.
Training on occupational health and safety topics such as confined spaces, working at height, Lock Out Tag Out (LOTO), Forklift Operations, Material Handling, Behaviour-Based Safety (BBS), and the use of personal protective gear is provided to all staff. Emergency preparedness is ensured through mock drills and awareness programmes. Annual medical check-ups are conducted for all employees and contractors, with preventive actions taken as needed. An on-site Occupational Health Centre (OHC) provides immediate medical aid.
In case of any safety-related incidents, incident investigations are conducted to understand the root causes of the incident. Learnings from this help to refine the safety procedures and training programmes, contributing to a safer working environment. The Lost Time Injury Frequency Rate (LTIFR), meaning that for every million hours worked during that period, was reduced from 1.34 in 2021-22 to 0.71 in 2022-23.
R&D Centres Ensuring Product Safety
PCBL places a significant emphasis on continuous research and development (R&D) of its products. Its R&D centres in Palej (Gujarat) and Ghislenghien (Belgium) take a proactive approach to anticipate and address emerging product safety and compliance requirements well before they become obligatory. The use of hazardous substances in products are restricted, ensuring that PCBL's products are not only consumer-safe but also environmentally responsible. Initiatives have been taken to optimise the properties of carbon black to improve the fuel efficiency of tyres, thereby impacting sustainability.
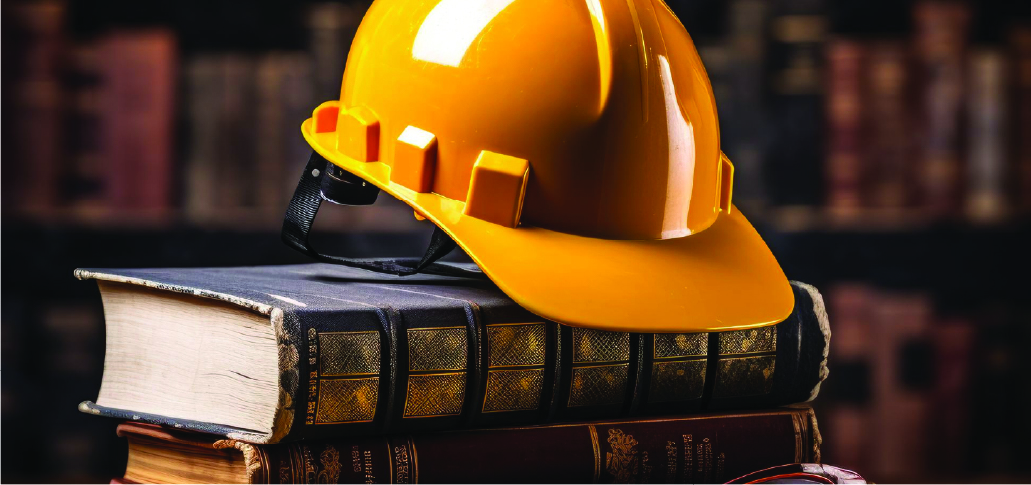
Collaborative Approach with Suppliers
The local medium-sized and small suppliers (LMS) are important for a company’s ecosystem. Acknowledging that LMS suppliers in the chemical sector often struggle due to inadequate infrastructure and resources, PCBL has come up with a growth plan for local production. This focuses on sourcing packaging, machinery, and spare parts locally. For example, PCBL sources paper bags from local suppliers for its automated packaging systems, rather than importing them. The company has also cultivated local vendors for machinery and spare parts, through knowledge and technology transfer. For example, PCBL is proactively involved in the local development of Air Pre-heater (APH), an essential equipment for carbon black production. The objective is to match international quality benchmarks while developing the capabilities of the local suppliers.
Collaborative efforts have been made with the suppliers to create a sustainable and ethical supply chain. PCBL’s Sustainable Procurement programme includes initiatives to assess the sustainability profiles of key suppliers. Suppliers are closely monitored to evaluate their practices, which involve reviewing their environmental, social, and ethical practices. This also includes training sessions, workshops, and communication initiatives to ensure that suppliers understand the importance of sustainability in the supply chain. A ‘Supplier Code of Conduct’ has been established, setting clear standards aligned with internationally-accepted sustainability principles such as the Sustainable Development Goals (SDGs) and UNGC-CDP Principles. The suppliers engaged in business with PCBL are expected to adhere to these standards, which are communicated and enforced through the collaboration process.
Providing an Inclusive Work-Environment
PCBL focuses on providing an inclusive and welcoming environment for all its employees. The company promotes equal rights for all employees without discrimination based on factors such as origin, nationality, religion, race, disability, gender, age, or sexual orientation. Special care is taken when assigning jobs to ensure that employees' physical limitations do not hinder their performance or career aspirations. PCBL offices are equipped with the necessary infrastructure like ramps, elevators, specially-designed washrooms etc., to ensure easy access for individuals with disabilities. This includes ramps, specially designed toilets, and elevators to accommodate physically challenged employees, creating an inclusive physical environment.
PCBL offers employees the option to submit their grievances through an AI chatbot called Leena. The chatbot administers surveys to employees and captures their mood scores. It helps in gathering feedback and identifying areas for improvement. There are also grievance and suggestion boxes placed in prominent locations within the workplace. Employees can use these boxes to submit their concerns anonymously. These concerns are then addressed by the plant HR.
PCBL has a well-defined grievance resolution process to address employee concerns and issues. The employee can reach out to their immediate supervisor, sectional head, or head of the department (HOD) depending on the nature and severity of the issue. If the concern is not resolved at the first level, the employee can escalate it to the next level, which can be the Unit Head. If the issue still remains unresolved, the employee can involve the Human Resources (HR) department.
The company conducts quarterly townhall meetings chaired by the Plant Head. These meetings provide a platform for employees to raise concerns, if any. The Plant Head and management team use these meetings to address and resolve issues, fostering open communication.

Universal Learnings
- Creating Workplace Safety Through Training and Audits - Training sessions, safety briefings, and visual displays about safety can significantly reduce workplace incidents. Regular internal and external audits can help in proactively assessing risks and taking appropriate corrective actions.
- Implementing Incident Reporting and Learning Systems - A reporting system, helps in capturing and learning from both adverse events and near misses. Post-incident evaluations can offer critical insights into procedural gaps and help in refining future safety measures.
- Driving Innovation & Compliance Through R&D Investments - Investing in R&D not only furthers innovation but also allows the company to stay ahead of compliance requirements.
- Strengthening Supply Chain Resilience & Quality through Local Supplier Development - Investing in the development of local suppliers can yield significant benefits, such as reduced costs and increased supply chain resilience. Sharing technology and expertise with local suppliers can elevate the quality of the local supply chain, making it competitive on an international level.
- Facilitating Effective Communication & Issue Resolution - Maintaining open channels of communication with employees and suppliers allows for easy identification of issues and quick resolution, and ensures that everyone is aligned with the company's objectives.
- Leveraging Digital Platforms for Bias-Free Employee Feedback and Grievance Handling - Utilising digital platforms like chatbots can be an effective way to collect employee grievances and feedback, making it easier for management to address concerns without bias.
The Governance Pillar - How PCBL's Governance Impacts its Entire Ecosystem
The Governance pillar of ESG is accountable for monitoring how a company approaches its environmental, social, and governance responsibilities. For example, for monitoring the Environmental pillar, the governance might include policies on sustainable resource use, waste management, and carbon footprint reduction. The Social pillar, might have governance policies for maintaining ethical labour practices, community engagement, and customer satisfaction. The Governance pillar is spear-headed by the senior management of a company, comprising the board of directors, senior management, and other stakeholders, who take a coordinated approach to set policies, ensure accountability, and monitor performance in these key areas.
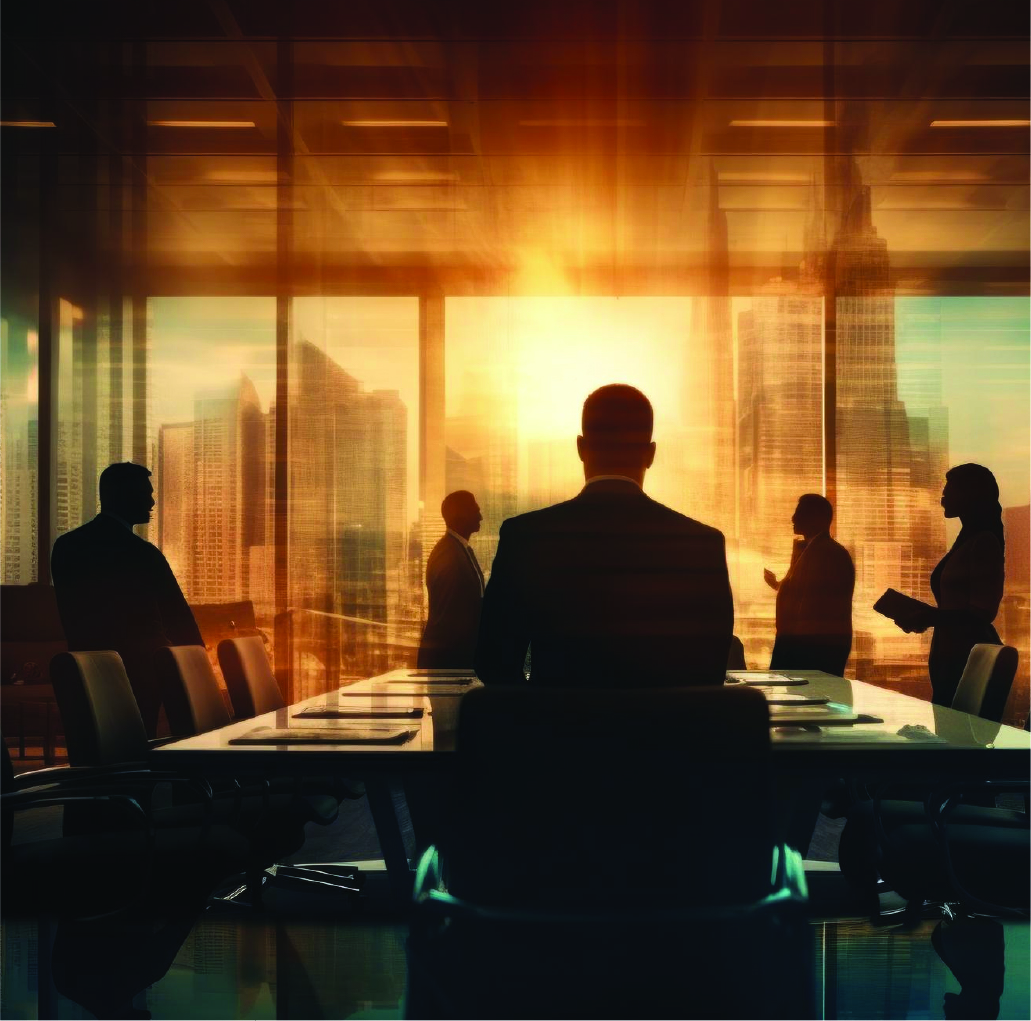
Involvement of leadership
PCBL’s commitment to ESG is meticulously overseen by various committees under the Management and Board of Directors of PCBL. These specialised committees, such as auditing, sustainability, risk management, and corporate social responsibility (CSR), are responsible for ensuring the incorporation of ESG principles across the organisation. They routinely scrutinise the ESG performance, pinpoint areas for enhancement, and formulate strategies to elevate the sustainability, social responsibility, and corporate governance standards. They also maintain ongoing dialogue with the stakeholders—ranging from investors and shareholders to community members—to collect insights for its ESG initiatives. Inputs from stakeholders are channelled to board-level committees for review, integrated into strategies, and communicated back to the stakeholders.
Effective governance of ESG factors not only serves to mitigate risks but also offer competitive advantages, enhancing reputation and stakeholder relationships. Companies with strong ESG governance are often seen as more sustainable and resilient in the long term, making them attractive to both investors and customers alike. By maintaining strong governance structures and practices, PCBL fosters a culture of integrity and compliance, thereby creating a resilient and sustainable business environment.
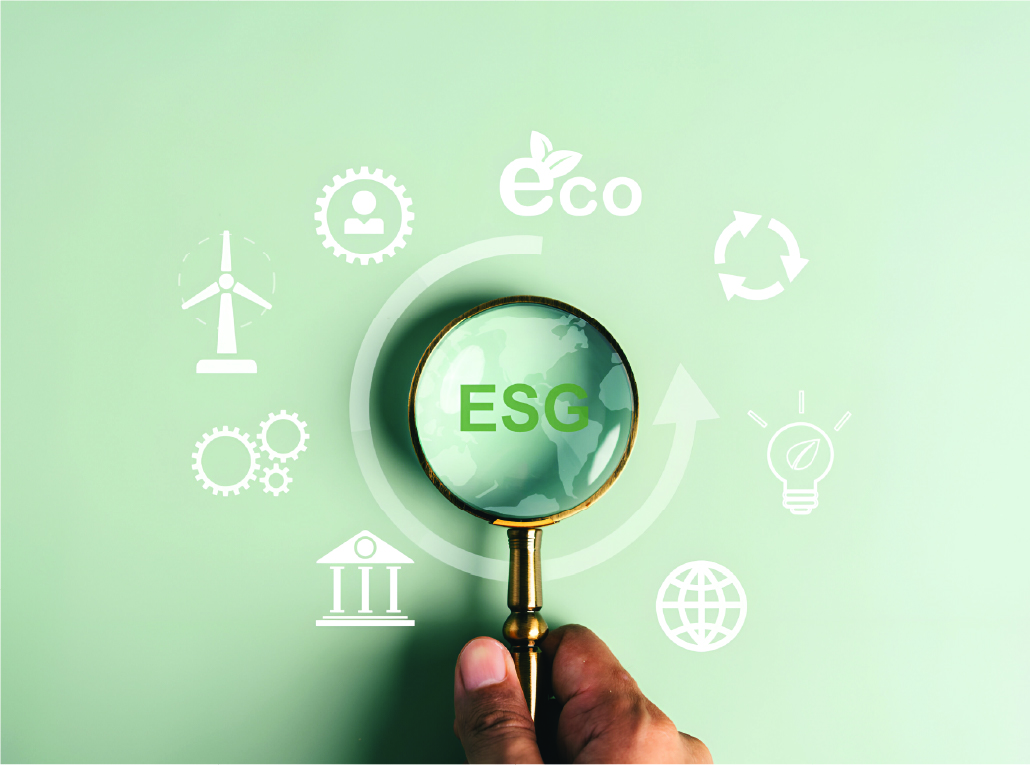
Universal Learnings
- A strong governance framework begins with the leadership of an organisation. Boards and senior management need to be aligned and committed to ESG principles, steering the organisation in the right direction.
- Setting up specialized committees is crucial for focused and effective governance. These committees not only monitor the performance but also suggest strategies for improvement, enhancing accountability and transparency.
- The policies need to be regularly reviewed and adjusted as necessary to ensure alignment with wider sustainability objectives.
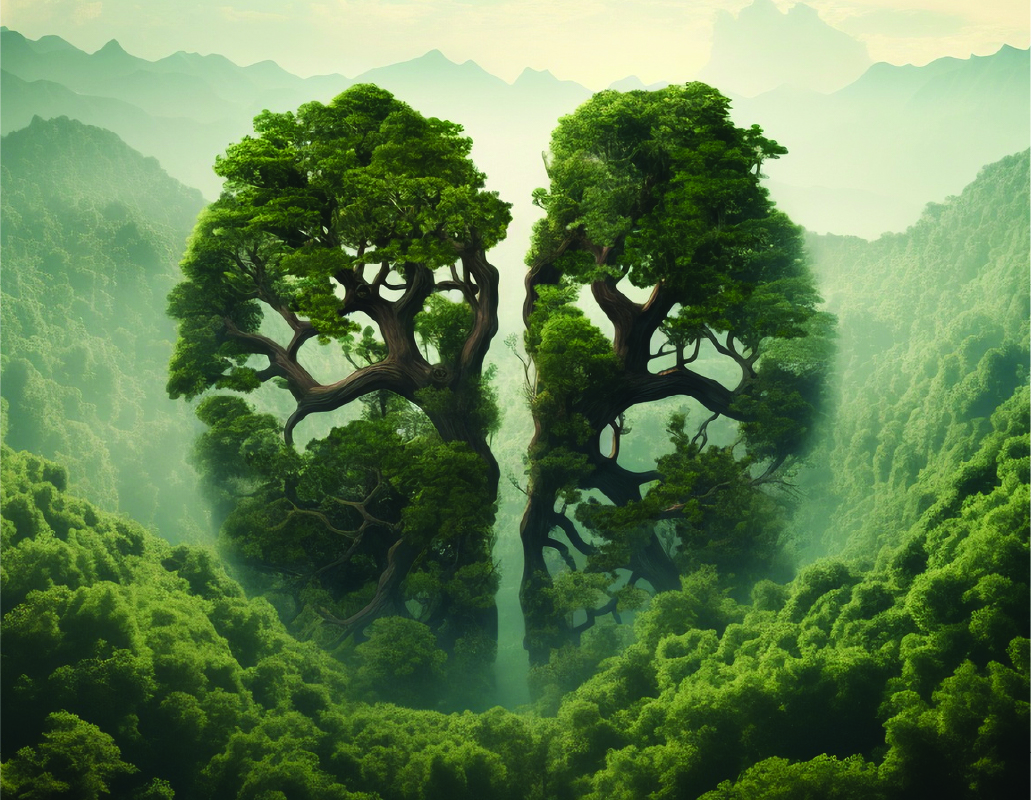
Conclusion
Navigating the complexities of today's business landscape necessitates a concerted focus on ESG principles. From investing in energy-efficient technologies and waste-to-resource conversion, PCBL's initiatives showcase its commitment to sustainable practices. Additionally, the company’s investment in Research & Development (R&D) has catalysed innovations that further its sustainability goals. These advancements also have the potential to shape industry standards, providing a roadmap for other companies seeking to improve their own ESG.
In the future, PCBL looks to significantly augment its ESG efforts by setting ambitious net-zero carbon targets. Further investments in R&D could drive innovation in eco-friendly products, while leveraging technologies like artificial intelligence and big data might help in enhancing operational and environmental efficiency. Employee education on sustainability would further solidify the company's ESG credentials.
For more information, please get in touch with: